Veredlung
Kalzinieren
Im Prozess des Brennens, fachsprachlich kalzinieren genannt, entsteht aus dem Calciumsulfat-Dihydrat (CaSO4·2H2O) unter Zusatz von Energie abbindefähiger Gips, vor allem in der Form von Calciumsulfat-Halbhydrat (CaSO4·½H2O). Ein gebrannter und damit abbindefähiger Gips kann mit Zugabewasser angerührt und zu Baustoffen, z.B. Gipsplatten, oder Bauteilen, z.B. Gipsputz, verarbeitet werden. Während des Austrocknens kehrt sich der Brennvorgang faktisch um: aus Calciumsulfat-Halbhydrat wird mit einem Teil des Wassers wieder Calciumsulfat-Dihydrat, das sich jetzt jedoch in der gewünschten Form befindet. Das beim Kalzinieren verwendete Brennaggregat, vor allem die Brenntemperatur entscheiden darüber über die Qualität und damit über die künftige Art der Anwendung des Bindemittels Gips.
Zur Herstellung von Stuckgips (Niederbrandgips) ist die Verwendung von Drehrohröfen weit verbreitet. Darin können im Gleichstromverfahren bei Temperaturen von 120 bis 180 °C bis zu 600 t Stuckgips in 24 Stunden erzeugt werden. Ein anderes häufig eingesetztes Aggregat zum Brennen von Stuckgips ist der sogenannte Kocher mit einem Fassungsvermögen bis zu 40 t. Eine dritte Möglichkeit zur Herstellung von Stuckgips bietet schließlich die Mahlbrennanlage, in der der Rohgips gemahlen, getrocknet und zu Stuckgips gebrannt wird. Auch eine Kombination mit einem Kocher ist üblich.
Auf TrägergasBrennanlagen können wechselweise Stuckgips oder Mehrphasengips gebrannt werden. Beim Mehrphasengips wird der Niederbrandgips in der ersten Brennstufe bei etwa 250 °C und der Hochbrandgips in der zweiten Brennstufe bei etwa 500 °C gebrannt. Soll nur Niederbrandgips (Stuckgips) hergestellt werden, durchläuft der Materialstrom ungeteilt die NiederbrandBrennstufe. Es gibt auch TrägergasBrennanlagen zur Erzeugung von reinem Anhydrit II.
Ein bewährtes Aggregat zur Herstellung von Hochbrandgips ist der Rostbandofen. Der Rohgips wird dort in verschiedenen Korngruppen mit zunehmender Korngröße (5 bis 60 mm) auf das sich kontinuierlich bewegende Rostband gegeben. Dabei erhitzt sich die obere Gipsschicht bis auf etwa 700 °C, im unteren Teil auf etwa 300 °C.
Nach einem grundsätzlich anderen Prinzip arbeiten die Verfahren zur Herstellung von α-Halbhydrat-Gips. Diese Modifikation des CalciumsulfatHalbhydrats wird unter Druck in Autoklaven bei Temperaturen im Bereich von 100 bis 150 °C hergestellt.
Newsletter Anmeldung
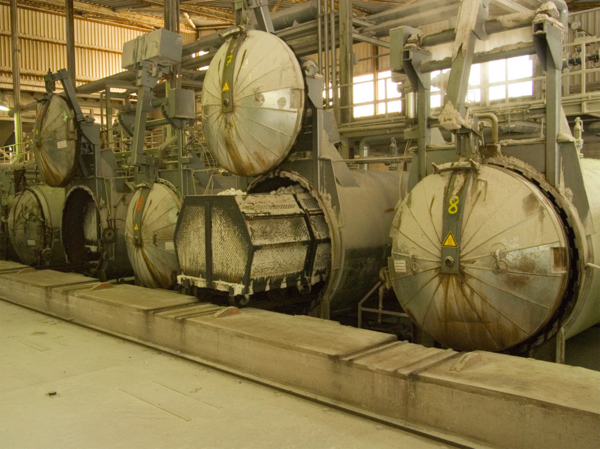